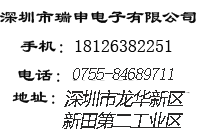
Injection molding an IC into a connector or consumable item
Exceeding the critical temperature
If the temperature of the plastic is too high when entering the mold, the solder that holds the IC in place softens or liquefie工字电感器s. As this hot plastic enters the mold cavity it can push the IC away from the pads on the substrate. Solder can protrude from the mold or short IC terminals, making the end product unusable or unreliable. Therefore, choosing the right temperature is a very critical step.
Nevertheless, there could be situations that require a plastic with a processing temperature above the solder melting point. In that case, one can consider two molding steps: first, use a plastic that stays below the critical temperature; second, use the plastic that requires the otherwise unacceptable temperature. Thus, with properly chosen dimensions and a well-timed temperature profile, the thermal inertia of the first layer protects the IC from the excess heat of the second molding step.
Real-world example
Application note 47021 features a DB9 connector with an embedded TO92-packaged 1插件电感-Wire® device. In this case, two of the DB9 pins are crimped to the IO and GND leads of the TO92 package. The NC (not connected) lead is cut off. This construction maximizes the choice of plastics since no solder is involved. Figure 2 shows the same connector before molding. The TO92 package is easily recognized.
Figure 2. DB9 connector with embedded TO92 1-Wire device before injection molding.
Conclusion
Injection molding is the method of choice to embed ICs in medical sensors and consumables. Special care is required when selecting the plastic material since its processing temperature must be low enough not to soften or liquefy the solder that attaches the IC to a substrate. Plastic materials are not equally suited for the sterilization required by medical applications. Consequently, only few of the sterilization methods are compatible with both the plastic material and ICs.
References
- See Maxim application note 4702, "Easily add memory, security, monitoring, and control to medical sensors and consumables," and application note 4623, "Smart cable aids quality control and authentication."
- Injection molding, http://en.wikipedia.org/wiki/Injection_molding
- For further reading, see Maxim application note 4132, "Atta工字电感chment methods for the electro-mechani一体电感cal SFN package."
- For examples of polymers best suited for the process, go t http://en.wikipedia.org/wiki/Injection_molding.
- For a discussion of the Characteristics of Various Plastic Materials, go t http://www.fcs.com.tw/webtop/FAQ_EN/index.phtml?action=browse&id=170&StoreID=9&, Fu Chun Shin Machinery Manufacture Co. Ltd.
- Choosing the Correct Thermoplastic Composite, RTP Company, at: http://www.thomasnet.com/white-papers/abstract/100711/choosing-the-correct-thermoplastic-composite.html.
- Selection of Materials for Medical Applications, RTP Company, at: http://www.thomasnet.com/white-papers/abstract/100710/selection-of-materials-for-medical-applications.html.
- Sterilization of Plastics, Zeus Industrial Products, at: http://www.thomasnet.com/white-papers/abstract/101488/sterilization-of-plastics.html.
- Gaseous Chlorine Dioxide and the Myth of Corrosion at: http://www.clordisys.com/MythOfCorrosion.pdf.
- Material Compatibility with Vaporized Hydrogen Peroxide (VHP®) Sterilization, http://www.steris.com/media/PDF/spacedecon/pharmaSolutions/point%20of%20manufacture%20mat%20comp%20pharma%20case%20study%202.pdf.
- Injection molding Processing Conditions for RTP Spe电感式传感器cial塑封电感器ty Compounds, RTP Company, at: http://www.rtpcompany.com/info/processing/index.htm.
锂离子电池智能充电器硬件的设计 锂离子电池具有较高的能量重量和能量体积比,无记忆效应,可重复充电次数多,使用寿命长,价格也越来越低。一个良好的充电器可使电池具有较长的寿命。利用C8051F310单片机设计的智能充电器,具有较高的测
基于LLC隔离的光伏并网逆变器设计方案0 引言随着光伏行业的蓬勃发展,光伏并网发电已经成为光伏发电领域研究和发展的最新亮点。光伏并网逆变器作为光伏发电系统的核心,对提高整个光伏发电系统的效率、可靠性、以及整个系统的使用寿命、降低成本至关重
一种锂离子智能充电器的设计与实现摘要:本文介绍了由MAXIM公司生产的一种新型充电器件MAX1757构成的1~3节锂离子电池充电器的工作原理和充电过程,并在此基础上给出了该充电器的工作流程及参数设置;最后简要阐述了PWM控制器的工作